When you’re dreaming of that perfect mountain home nestled in the Colorado Rockies, the path to getting there isn’t as straightforward as it used to be.
Between Breckenridge’s soaring property values and Vail’s limited building seasons, mountain homeowners are increasingly weighing their options between traditional stick-built homes and modern modular construction.
Let’s explore how these choices stack up in Colorado’s unique mountain environment.
The Mountain Challenge
Weather Realities
Building in Colorado’s mountains isn’t like construction anywhere else.
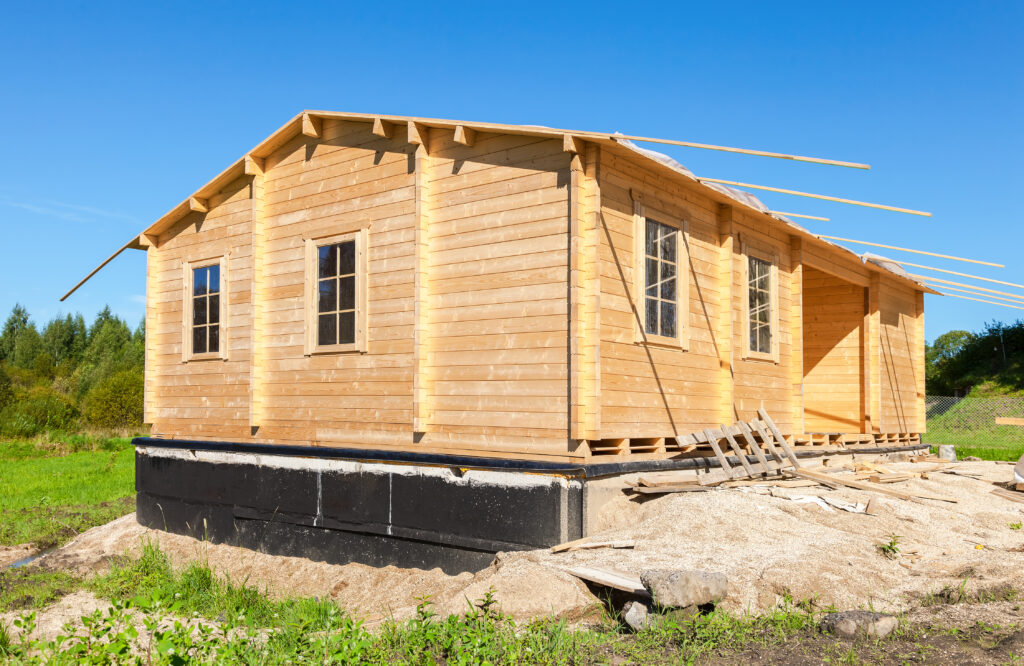
Modular Homes = Cost Savings!
When you’re dealing with unpredictable snowstorms in May and early freezes in September, your building window gets squeezed tight. Traditional construction might stretch through multiple seasons, while modular homes can often be set and weathertight before the first snowfall.
Elevation Considerations
At 8,000+ feet, every construction decision carries extra weight. The thin air affects everything from concrete curing times to worker productivity. Here’s where the indoor construction environment of modular homes starts to show its advantages, with crews working at sea level in controlled conditions.
Breaking Down the Numbers
Labor Costs
Let’s talk real numbers. In mountain towns like Steamboat Springs or Telluride, skilled labor comes at a premium. Traditional builds might require housing your crew for months, while modular construction significantly reduces on-site labor time. One Summit County builder reported labor savings of up to 30% on modular projects compared to traditional builds.
Material Efficiency
Traditional construction in the mountains often means ordering extra materials to account for weather damage and difficult storage conditions. Modular construction’s factory setting virtually eliminates weather-related material waste, typically saving 15-20% on material costs.
Timeline Impact
Season Sensitivity
In places like Winter Park or Crested Butte, building season can be as short as four months. Traditional construction might span multiple seasons, increasing costs with each delay. Modular homes can often be set and finished within one season, dramatically reducing timeline-related expenses.
Financial Implications
Every month of construction means another mortgage payment, more contractor overhead, and extended equipment rentals. Mountain builds that stretch into multiple seasons can add 20-30% to the final cost just in carrying charges and extended timelines.
Quality Considerations
Mountain-Specific Engineering
Both construction methods must meet Colorado’s strict mountain building codes, but they approach it differently:
Traditional Builds:
- Custom engineering for each site
- Field adjustments for specific conditions
- Higher chance of weather-related issues during construction
Modular Construction:
- Factory-engineered for mountain conditions
- Consistent quality control
- Weather-protected construction process
Site Impact
Environmental Footprint
Colorado mountain communities are increasingly environmentally conscious. Consider these factors:
Traditional Construction:
- Extended site disruption
- More construction traffic
- Greater impact on local wildlife
Modular Approach:
- Reduced site time
- Fewer deliveries
- Minimized local environmental impact
Access Challenges
Mountain lots often present access challenges. Traditional builds might require months of heavy equipment access, while modular homes typically need just a few days of crane access for setting. In towns like Aspen or Telluride, where streets are narrow and neighbors are close, this can mean significant cost savings in access fees and logistics.
Long-Term Value
Energy Efficiency
Colorado’s extreme mountain climate makes energy efficiency crucial. Modular homes often show advantages here:
- Factory-precise insulation installation
- Tighter building envelope
- More consistent quality control in energy-critical areas
Maintenance Costs
The first five years often tell the story:
Traditional Builds:
- More settling issues in mountain soils
- Higher likelihood of weather-related problems during construction
- Variable quality depending on available local labor
Modular Homes:
- Less settling due to factory-controlled construction
- Weather-protected assembly process
- Consistent construction quality
The Hidden Savings
Insurance Considerations
Insurance companies are taking notice of modular construction’s advantages:
- Lower risk during construction
- Better quality control documentation
- Potential premium savings
Financing Benefits
Some lenders are offering preferential terms for modular construction:
- Shorter construction loan periods
- More predictable completion dates
- Reduced risk of weather delays
Making Your Decision
Project-Specific Factors
Consider your specific situation:
- Site accessibility
- Local labor availability
- Building season length
- Budget constraints
- Timeline requirements
Local Considerations
Each mountain community has its own factors:
- Architectural review board requirements
- Local contractor availability
- Zoning restrictions
- HOA considerations
The choice between modular and traditional construction in Colorado’s mountains isn’t just about initial cost – it’s about understanding the total impact on your project’s bottom line. While modular construction often shows significant upfront savings, the real value comes from reduced build time, lower weather risk, and more predictable outcomes.
For many mountain homeowners, the combination of cost savings, shorter construction timelines, and reduced environmental impact makes modular construction an increasingly attractive option. However, each project needs careful evaluation based on specific site conditions, local regulations, and personal preferences.
Remember, whether you choose traditional or modular construction, success in Colorado mountain building comes down to thorough planning, understanding local conditions, and working with experienced professionals who know the unique challenges of high-altitude construction.